
Nailstone Colliery
Photos and Stories
Leicestershire Coal Mine
Nailstone Colliery
The originator of this colliery may have been J.J. Ellis but this does not appear to be known for certain. What is known is that he owned the colliery in 1866 but he sold out in 1875. Thereafter followed a very shaky period and the colliery closed in 1876. It was working again under new ownership by 1883. When this owner died in 1887 the colliery was taken over by the Nailstone Colliery Company.
Shafts– Shaft sinking commenced in 1862, two shafts being sunk. The downcast shaft was 10 feet diameter and the upcast shaft 10 yards away from the downcast, was 8 feet diameter. The Upper Main Seam was reached at 143 yards from the surface, the shafts having initially passed through some 80 yards of New Red Sandstones. The lower part of the sandstones gave out water, which continued after the sinking was completed, the rate being about 70 gallons per minute.
In 1868 the shafts were deepened to 205 yards to win the Lower Main Seam (or Roaster Seam). Subsequently the upcast shaft was further deepened to 283 yards but without finding any workable seams.
Additionally to the above two shafts there was a ladder shaft 20 yards away from the downcast and this provided access from one shaft to the other.
Winding– A tandem headgear was erected over the shafts, allowing one winding engine to serve both. From photographic evidence, the original winding engine house appeared to house a vertical (crank overhead) winding engine.
In 1874 a horizontal winding engine was installed, this being placed in a new house located behind the original. The new winding engine had twin cylinders, 26in. x 48in. fitted with slide valves operated by Stephenson link motion. The winding drum was stepped to accommodate the two different winding depths. One side was 10 feet diameter for the downcast shaft and the other side was 14 feet diameter for the upcast shaft. Winding was from the Upper Main and Lower Main seams respectively. The makers of the engine were Messrs. Death & Ellwood of Leicester.
The engine wound a single cage in each shaft, the cages having two decks each carrying a single tub. The winding ropes were one and one eighth inches diameter and fitted with King detaching hooks. Two conductors were provided to guide each cage.
Possibly in 1921, the engine was rebuilt by the Worsley Mesnes Ironworks, Wigan, who fitted new cylinders, 24in. x 48in. which had inside admission piston valves. At some date the engine was fitted with a parallel winding drum with curved post brakes operating on a brake path on each side of the drum. The brakes were actuated by a Melling’s (Worsley Mesnes) brake engine. Winding depth was 170 yards. The engine served until the colliery was closed for coal winding in 1967.
The original tandem headgear constructed in timber was replaced about 1898 by a new structure built in pitch pine and 50 feet in height. Latterly quite a massive steel tandem headgear was erected.
Underground Haulage– Two steam haulage engines were placed at the surface, serving the Main and Lower Main seams respectively. The Upper Main engine was a twin cylinder horizontal with 12in. x 24in. cylinders. This engine drove two rope drums, each 4ft. diameter with a toothed clutch between them to connect the drive to one drum or the other. Both drums each served a single rope direct haulage system. The ropes passed down the downcast shaft each encased in timber trunking. One rope hauled on the East Incline, 800 yards in length bringing up ten tubs at a time. Empty runs of tubs descended by gravity, the dip being 1 in 14 to the east.
The second rope was employed on a roadway 700 yards long in a north direction. This roadway was undulating due to negotiating faults in the strata. The rope was used to haul tubs where the road was on a rising gradient outbye. Elsewhere, horses were used and there was also a self-acting incline 200 yards in length.
The Lower Main haulage engine was a 16in. x 36in. twin cylinder horizontal geared 3 to 1 to the second motion shaft. In addition to its haulage duties, the engine acted as an emergency winder for the upcast shaft. For this duty an 8 feet diameter rope drum was fitted to the second motion shaft. A 6ft. diameter Clifton pulley was provided on the second motion shaft which operated an endless rope haulage system. The haulage rope passed down the upcast shaft to the Lower Main seam where it operated on an east road on the dip for a distance of 500 yards. The tubs were run in “gangs” of two, attached to the rope by Smallman clips.
Ventilation– Until 1899, ventilation was provided by an underground furnace which circulated approximately 45,000 cubic feet of air per minute against a mine resistance of 0.7 inches water gauge.
In 1899 a centrifugal fan was installed, made by Walker Bros., Pagefield Ironworks, Wigan. The fan was 9ft. diameter by 3ft. 6in. wide and was driven by a Walker Bros. single cylinder horizontal engine. The cylinder was 15in. x 30in. fitted with an ordinary slide valve for steam distribution. A 12 feet diameter flywheel was mounted on the crankshaft and drove through a leather belt to a 3ft. diameter pulley on the fan shaft.
Pumping– There was no pumping as such. Water feeding into the shafts was led to the respective sumps where it was allowed to accumulate. The water was then raised by the winding engine at night. Wheeled tanks made of wrought iron were used which ran into the cages. The tanks were arranged to be self-filling at the shaft bottom and self-discharging at the top. Tank capacity was 325 gallons in the upcast shaft and 459 gallons in the downcast. Winding took place for about four hours.
Boilers– Near to the end of the 19th. century there were six egg-ended boilers at the colliery plus two more which served the nearby brickworks. Working pressure for all the boilers was 50 psi. and three boilers were fitted with Meldrum’s forced draught furnaces. The chimney serving the colliery boilers was 90 feet in height and 9ft. inside diameter.
Underground Working– At the time of a 1899 Colliery Guardian survey the Upper Main and Lower Main seams were the only seams being worked. Seams above the Upper Main were hardly touched. Longwall working was used in both seams for coal extraction and the general dip of the seams was 1 in 14 to the east. The tubs were brought to the face of the working stalls for filling and were hauled by ponies to the main rope haulage or horse haulage roads. Forks were used for filling the tubs and the slack was left in the waste of gob. The Lower Main seam was liable to spontaneous combustion and the wastes or gobs had to be watched for out-breaks of fires.
Open flame lighting was generally in use, the working stalls being tested for gas in the mornings by safety lamps. In the Lower Main a safety lamp was kept burning in the working stalls at the highest point as a warning of the presence of, firedamp.
A general section of the Upper Main seam was a roof of strong stone bind. The top coal of 7in. to 9in. was inferior and left up. Below this was hard coal (suitable for locomotives) 3ft. 6in. thick and below this a bottom coal 1ft. 2in thick, which was of second quality. Below the coal was fireclay, some of which was used for making firebricks.
A general section of the Lower Main seam was that above the coal was a bed of fireclay 3ft. to 14ft. thick. The coal seam comprised 9 inches of “spires” a hard coal which was left up to form the roof of the workings. Below this was 3ft. 11in. of best house coal followed by 1ft. 4in. of inferior coal. A band of mixed coal and stone 1 foot thick lay immediately below the coals and this was taken out and used for packing the wastes (or gob). Under this band lay a further bed of fireclay.
Coal Preparation– At the time of the Colliery Guardian report on the colliery in 1899, on arriving at the coal screening plant the best pieces of coal were lifted off the tubs and placed directly into railway wagons. Other coal was tipped on to fixed and shaking screens where it was graded into hand-picked cobbles, screened cobbles, large nuts, small nuts and slack. The cobbles and large nuts were cleaned by hand picking as they passed over the screens and chutes.
In addition to local coal sales, there was a London market for house and other coals. The London & North Western Railway purchased 30,000 tons per annum as locomotive coal and some exports were made from King’s Lynn.
Brickworks– There was a brickworks associated with the colliery making firebricks, red bricks and earthenware drainage pipes. A good quality clay found near to the colliery was used in the manufacture of the red bricks and pipes. Much of the brick making machinery had been made by Wootton Bros. of Coalville.
Later Developments– The foregoing notes largely refer to the colliery as it was at the time of a Colliery Guardian report in 1899.
As mentioned previously, the winding engine was rebuilt, including new cylinders suitable for a higher working steam pressure. This rebuild would possibly be associated with the installation of new Lancashire boilers having a working pressure considerably higher than the 50 psi of the old egg-enders.
Other coal seams were developed, a necessity as the Upper and Lower Main seams would in due course have become exhausted. In the 1950’s the colliery was working the Middle Lount and the Yard seams. Coal production ceased at the colliery in 1967.
It became National Coal Board policy in this area to sink drifts for bringing coal to the surface and to abandon the use of shafts for this purpose. A drift was put down at Nailstone to enable the output of Bagworth Colliery to be brought out at Nailstone. Ellistown and South Leicester collieries also became linked and the whole of the output was brought to the surface at Nailstone. The Nailstone surface area thus became a major centre for coal preparation and distribution. These operations finally ceased in 1991 when Bagworth, the last working colliery, was closed.
We would like to thank the Northern Mine Research Society for their kind permission to use the above information about Nailstone. Their website and further information can be found....
We Invite you to get involved in what we want to achieve, share your stories and experience so we can keep them for future generations.
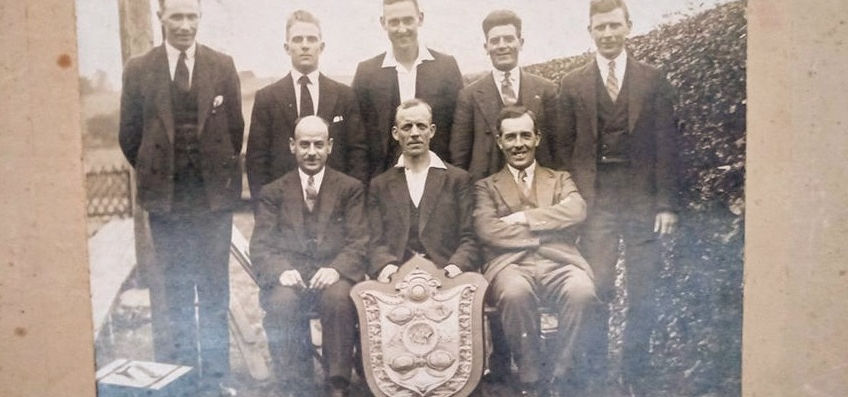